The Evolution and Importance of Plastic Automobile Parts Mold
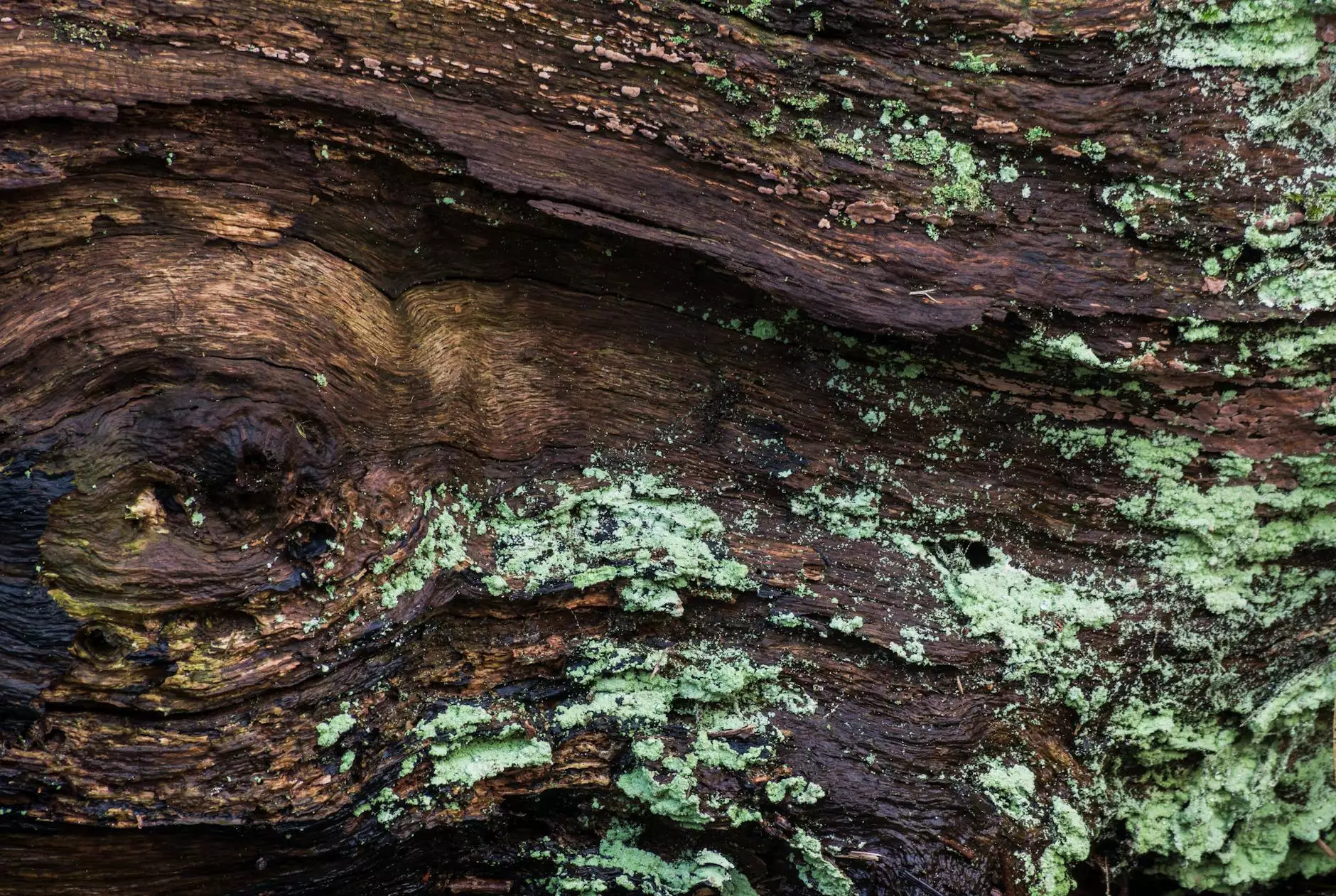
In the modern automotive industry, the utilization of plastic automobile parts mold has become instrumental in the production of efficient and durable vehicles. As technology advances, the integration of sophisticated techniques has transformed how automobile parts are designed, manufactured, and utilized across the industry. This article delves deep into the significance of plastic molds, their manufacturing processes, and their impact on the evolution of automobiles, backed by industry insights from Hanking Mould, a premier plastic mold maker and injection mould manufacturer.
The Role of Plastic in the Automotive Industry
The automotive industry is experiencing a significant shift, favoring plastic components over traditional metal parts. The reasons for this transition are multifaceted:
- Weight Reduction: Plastic parts are significantly lighter than their metal counterparts, contributing to improved fuel efficiency and performance.
- Corrosion Resistance: Plastics do not corrode like metals, enhancing the longevity of automotive parts.
- Design Flexibility: The malleability of plastic allows for intricate designs that metals cannot easily replicate.
- Cost-Effectiveness: Producing plastic parts is often less costly due to lower raw material and processing costs.
The Manufacturing Process of Plastic Automobile Parts Mold
Understanding the manufacturing process of plastic automobile parts molds is crucial for grasping their significance in the automotive industry. The primary processes involved include:
1. Design and Prototyping
The first step in creating a plastic mold begins with the design phase. Engineers and designers utilize advanced software to create 3D models of the parts. Prototyping techniques, such as 3D printing, allow for quick testing of designs before actual production.
2. Mold Fabrication
Once a design is finalized, the next step is the fabrication of the mold. This process involves the use of precision machining and cutting tools to create the mold that will shape the plastic parts. High-quality materials are essential to ensure the molds can withstand repeated use.
3. Injection Molding Process
In the injection molding process, plastic pellets are heated until they melt and then injected under pressure into the mold cavity. After a cooling period, the newly formed plastic part is ejected from the mold. This process allows for high-volume production with consistent quality.
4. Quality Control and Testing
Quality control is a critical aspect of the manufacturing process. Parts are rigorously tested to ensure they meet industry standards and specifications. Techniques such as dimensional inspection and physical testing assess the integrity and performance of the parts.
Types of Plastic Materials Used in Automobile Parts
The choice of plastic material significantly impacts the performance, durability, and appearance of automobile parts. Commonly used plastics in the automotive industry include:
- Acrylonitrile Butadiene Styrene (ABS): Known for its strength and impact resistance, ABS is commonly used for interior parts and dashboards.
- Polypropylene (PP): This is a versatile, lightweight material used in bumpers and interior panels due to its high fatigue resistance.
- Polyamide (Nylon): Known for its heat and chemical resistance, Nylon is used in engine components and fuel systems.
- Polycarbonate (PC): This transparent plastic is favored for its toughness and is used in headlamp lenses and safety features.
Advantages of Using Plastic Automobile Parts Mold
There are numerous advantages to using plastic automobile parts molds in automotive manufacturing. Some of the key benefits include:
- Efficiency: The injection molding process allows for rapid production of parts, significantly reducing time-to-market for new vehicles.
- Consistency: Molds ensure a uniform quality of parts, minimizing defects and variations in production.
- Customization: Plastic molds can be designed to produce a wide range of shapes, allowing for innovative designs tailored to specific automotive needs.
- Reduced Environmental Impact: Modern plastic molding techniques often utilize recycled materials, leading to a smaller environmental footprint.
Challenges in the Plastic Molding Industry
While the use of plastic molds offers numerous benefits, there are challenges that manufacturers must navigate:
- Material Selection: Choosing the appropriate plastic material for specific applications can be complex, as different parts have varying requirements regarding strength, flexibility, and temperature resistance.
- Technological Advancements: Keeping up with rapid technological changes requires continuous investment in new machinery and training for staff.
- Recycling and Sustainability: Although recycling in the plastic industry is growing, manufacturers must develop effective strategies to minimize plastic waste and enhance sustainability efforts.
Future Developments in Plastic Mold Manufacturing
The future of plastic automobile parts mold manufacturing looks promising with continued technological advancements. Notable trends include:
- 3D Printing: This technology is expanding in the mold-making industry, allowing for faster prototyping and lower costs.
- Smart Manufacturing: The Internet of Things (IoT) is set to revolutionize production processes, enabling real-time monitoring and optimization.
- Integration of Sustainable Practices: Manufacturers are prioritizing eco-friendly practices, utilizing biodegradable plastics and improving recycling processes.
Conclusion: The Impact of Plastic Automobile Parts Mold on the Future of Automotive Manufacturing
The shift towards plastics in the automotive sector is reshaping the industry in profound ways. Plastic automobile parts molds offer unparalleled advantages in cost, weight, and design flexibility, making them indispensable in modern vehicle manufacturing. Companies like Hanking Mould are at the forefront of this transformation, providing high-quality molds that cater to the ever-evolving needs of the automotive market.
As the industry evolves, so too will the technologies and practices surrounding plastic mold manufacturing. Manufacturers must remain agile, embracing innovation while addressing the challenges of sustainability and quality standards. Ultimately, the continued advancement of plastic automobile parts molds will play a critical role in the future of automotive design and production, ensuring vehicles are not only efficient but also environmentally responsible.