The Comprehensive Guide to Plastic Molding in China
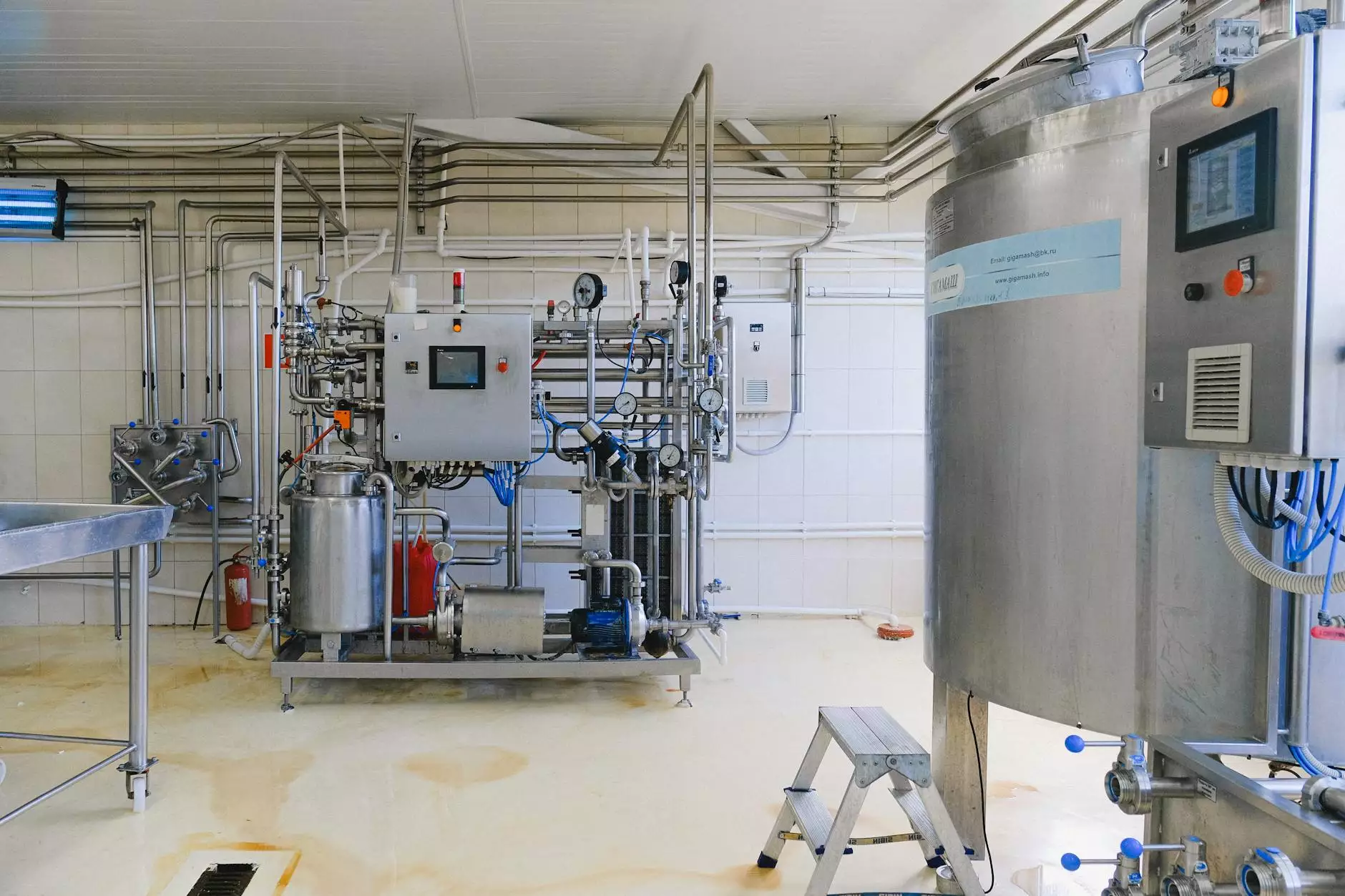
In the world of manufacturing, plastic molding in China has emerged as a pivotal sector, driving innovation and production capabilities across global markets. This article provides an extensive overview of the intricacies involved in plastic molding, its economic significance, and why China stands out as a leading hub in this field, especially focusing on plastic mold making and plastic injection mold manufacturing.
Understanding Plastic Molding
Plastic molding is a manufacturing process that involves shaping plastic materials into desired forms. There are several methods of plastic molding, each suitable for different applications. The most common types include:
- Injection Molding: A method where molten plastic is injected into a mold.
- Blow Molding: A process used to create hollow plastic parts.
- Extrusion Molding: A technique where plastic is formed into continuous shapes.
- Rotational Molding: A method that allows for the creation of large, hollow parts.
Of these, injection molding is the most widely utilized due to its efficiency, versatility, and capability to produce high volumes of complex parts.
The Rise of Plastic Molding in China
China has established itself as a titan in the global manufacturing landscape, underpinned by its rapid industrial growth and technological advancements. The reasons for the burgeoning success of plastic molding in China include:
1. Cost-Effectiveness
One of the most significant advantages of manufacturing in China is its cost efficiency. The labor and production costs are considerably lower compared to Western countries, allowing businesses to maintain competitive pricing. For companies looking to produce high-quality plastic parts, this translates into substantial savings.
2. Advanced Technology
Chinese manufacturers leverage cutting-edge technology and machinery to ensure precision and quality in their products. Modern plastic mold making equipment incorporates automation and advanced materials, significantly enhancing production capabilities.
3. Skilled Workforce
China boasts a large pool of skilled workers trained in various aspects of manufacturing and engineering, ensuring expertise in mold design and production processes.
4. Supply Chain Integration
The extensive supply chain network within China facilitates quick access to raw materials and components, in turn speeding up the production timeline and improving efficiency.
Exploring Plastic Mold Making
Plastic mold making is a crucial component of the manufacturing process, forming the foundation of high-quality molded products. This section will delve into the essential aspects of plastic mold making in China.
Design and Engineering
The initial stage of plastic mold making involves design and engineering. Skilled designers utilize CAD (Computer-Aided Design) software to create intricate designs that meet client specifications. These designs are then reviewed for manufacturability and potential performance issues.
Material Selection
The choice of material for molds is critical, as it affects the durability and performance of the end product. Common materials used in mold making include:
- Steel: Known for its durability, often used for longer production runs.
- Aluminum: Lightweight and cost-effective, suitable for shorter runs.
- Resin: Typically used for prototyping and low-volume production.
Machining and Fabrication
Once the design and materials are finalized, the fabrication process begins. This involves a series of machining processes, such as milling, drilling, and electrical discharge machining (EDM). Utilizing precise techniques ensures that molds meet exact specifications and provide high-quality finishes.
Mold Testing and Validation
After molds are created, rigorous testing is performed to guarantee their effectiveness in producing the desired parts. This stage often includes trial runs to detect any issues and make necessary adjustments before mass production.
The Process of Plastic Injection Molding
Plastic injection molding is a widely preferred technique for producing large quantities of identical parts. This section will outline the steps involved in the injection molding process.
1. Material Preparation
The process starts with the preparation of plastic pellets, which are melted down to a uniform temperature. The melted plastic is then injected into the mold cavity.
2. Injection
The molten plastic is injected under high pressure into the prepared mold. This step is crucial, as the pressure ensures that the material fills all the intricate details within the mold.
3. Cooling
Once the mold is filled, it is allowed to cool. Cooling times can vary based on the size and thickness of the part, and this step is essential to ensure that the plastic solidifies properly.
4. Demolding
After cooling, the mold opens, and the finished part is ejected. This component is then inspected for quality before it undergoes any post-processing, if required.
5. Finishing Touches
Depending on the end-use of the product, additional finishing processes may be necessary, such as trimming, painting, or assembling additional parts.
Quality Control in Plastic Molding
Quality control is paramount in the plastic molding industry. Manufacturers in China often adopt rigorous quality assurance methodologies to maintain high standards. This includes:
- Regular Inspections: Ongoing inspections throughout the manufacturing process help identify any defects early.
- Testing Protocols: Comprehensive testing methods ensure that produced parts meet industry standards and client requirements.
- Feedback Loops: Incorporating customer feedback into the manufacturing process allows for continuous improvement and innovation.
The Future of Plastic Molding in China
The landscape of plastic molding in China is ever-evolving. Future trends indicate a shift towards sustainable practices and advanced technologies, such as:
1. Sustainable Materials
The demand for environmentally friendly materials is on the rise. The industry is exploring bioplastics and other renewable resources to minimize environmental impact.
2. Automation and Smart Manufacturing
As the Fourth Industrial Revolution progresses, the adoption of automation and smart technologies in manufacturing is expected to enhance efficiency and reduce costs significantly.
3. Customization
With the increasing demand for personalized products, manufacturers are anticipated to focus on molding solutions that allow for customization without sacrificing efficiency.
Conclusion
In summary, the landscape of plastic molding in China is robust, characterized by innovation, cost-effectiveness, and an ever-growing talent pool. As businesses continue to seek high-quality, efficient, and customized solutions for their plastic parts, China remains at the forefront of the industry, particularly in plastic mold making and plastic injection mold manufacturing.
With a commitment to quality and advancements in technology, Chinese manufacturers are well-equipped to meet the evolving needs of the global market. Engaging with trusted partners like hanking-mould.com ensures that businesses can leverage these advantages to enhance their product offerings and remain competitive in the dynamic world of manufacturing.
plastic molding china