Enhancing Safety: The Importance of **Fume Cupboard Testing in Newport**
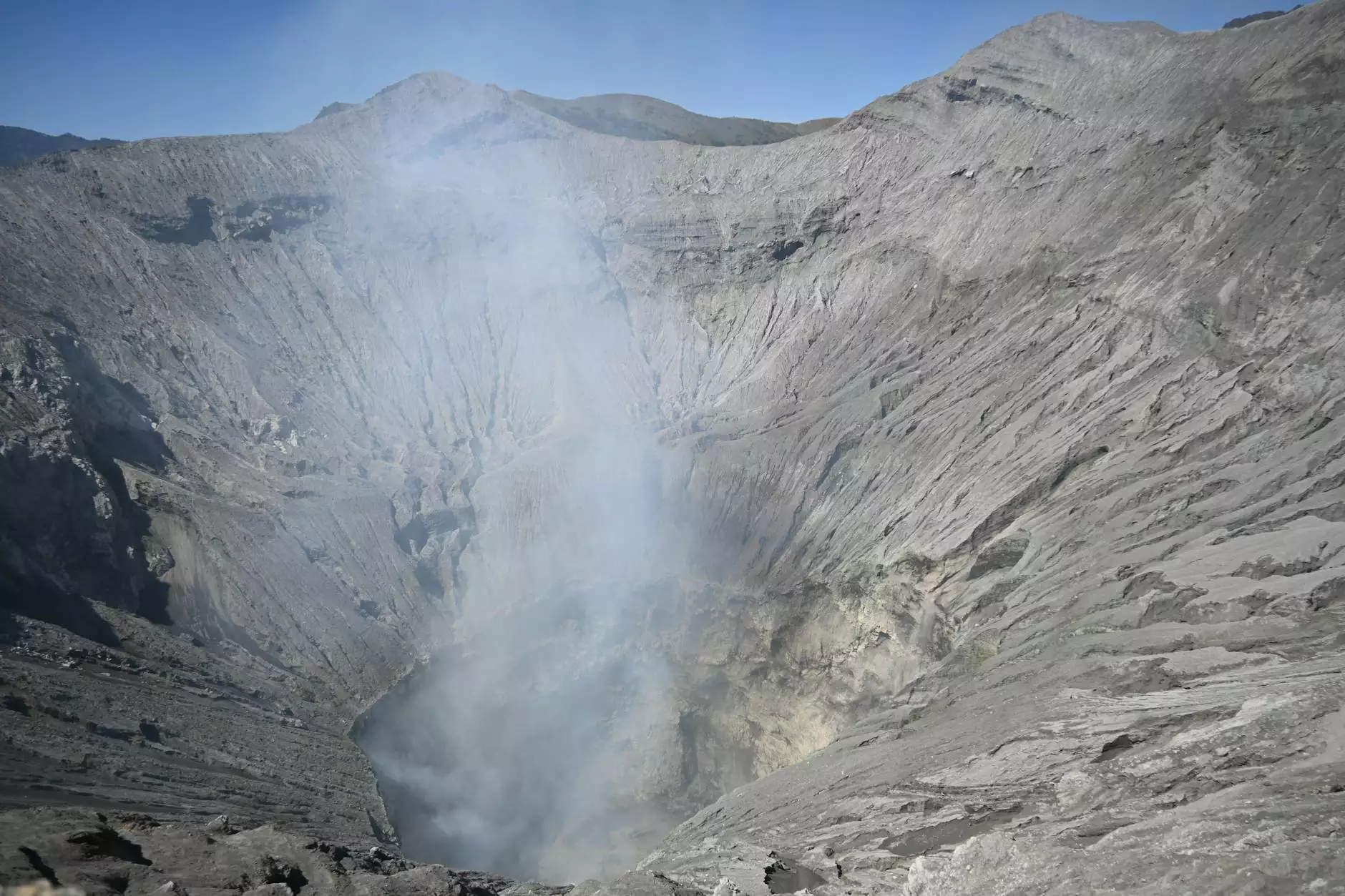
In the bustling arena of laboratory safety, the significance of fume cupboard testing cannot be overstated. Newport, a city known for its innovative industries and rich history, is home to a variety of laboratories and educational institutions that rely on fume cupboards to protect their workers and the environment. This article delves into the essential nature of fume cupboard testing, exploring its benefits, processes, and relevance to businesses in Newport, particularly those under the umbrella of Safe Plant UK.
What is a Fume Cupboard?
A fume cupboard, also known as a fume hood, is a ventilated enclosure designed to safely handle hazardous materials and chemicals. Its primary function is to remove noxious fumes, vapors, and dusts, thereby ensuring the safety of laboratory personnel. Proper functioning of a fume cupboard is critical; otherwise, it can lead to severe health risks and potential legal repercussions for businesses.
The Direct Benefits of Regular Fume Cupboard Testing
Comprehensive and regular fume cupboard testing offers numerous benefits for organizations operating within Newport:
- Disease Prevention: Protects laboratory staff from exposure to harmful substances.
- Environmental Protection: Reduces the risk of chemical spills and adverse environmental impact.
- Compliance: Ensures adherence to health and safety regulations, avoiding potential fines.
- Performance Assurance: Confirms that fume cupboards are functioning correctly and efficiently.
- Peace of Mind: Provides assurance to staff and management regarding safety measures in place.
Understanding the Fume Cupboard Testing Process
The testing process for fume cupboards is meticulous and should be carried out by qualified professionals, such as those from Safe Plant UK. Here’s a detailed look at what this process typically involves:
1. Initial Inspection
Before any testing begins, a thorough visual inspection is conducted. This includes checking for:
- Physical damage to the fume cupboard.
- Correct installation and sealing of all joints.
- Functionality of the sash and control mechanisms.
2. Airflow Testing
Airflow is the critical parameter that ensures safety in fume cupboards. This phase includes:
- Measuring the face velocity of the fume cupboard.
- Testing to ensure the airflow is within the safe limits, typically 0.5 to 1.0 meters per second.
- Identifying any obstructions or disturbances in airflow patterns.
3. Performance Verification
This step assesses how effectively the fume cupboard can contain fumes and prevent them from escaping into the laboratory:
- Use of smoke tests to visualize airflow patterns.
- Assessing the integrity of the fume cupboard under simulated conditions.
4. Documentation and Reporting
Once testing is complete, comprehensive documentation is provided, detailing:
- Test results and any alterations made.
- Recommendations for improvements or repairs if necessary.
- Follow-up testing schedules to ensure ongoing compliance.
The Role of Safe Plant UK in Fume Cupboard Testing
Safe Plant UK is a leading provider of safety and compliance solutions in Newport and across the UK. With a team of trained professionals and extensive experience in the field, Safe Plant UK ensures that your fume cupboard testing adheres to the highest safety standards. Their services not only encompass testing but also:
- Training: Offering workshops and training sessions for staff on proper fume cupboard use and maintenance.
- Consultation: Providing advice on the best practices for laboratory safety and risk management.
- Repairs and Maintenance: Ensuring fume cupboards are repaired and maintained to extend their lifespan and efficiency.
Regulatory Compliance and Legal Obligations
In the UK, there are strict regulations surrounding workplace safety, particularly in environments handling hazardous substances. Compliance with Health and Safety Executive (HSE) guidelines is imperative. Regular fume cupboard testing not only helps ensure safety but also aids businesses in meeting their legal obligations, thereby minimizing the risk of penalties or litigation.
Common Regulations Affecting Fume Cupboards
Some key regulations include:
- Control of Substances Hazardous to Health (COSHH): Requires employers to control substances that can be hazardous to health.
- Health and Safety at Work Act 1974: Mandates safe working practices and environments.
- Laboratory Safety Regulations: Detailed regulations specific to laboratories which include fume cupboard requirements.
Choosing the Right Service Provider for Fume Cupboard Testing
When selecting a service provider for fume cupboard testing in Newport, consider the following factors:
- Experience and Expertise: Choose a provider with a proven track record in laboratory safety.
- Certifications: Ensure they are certified and compliant with relevant industry standards.
- Comprehensive Services: Look for companies that provide a wide range of safety solutions, including training and repair services.
- Customer Reviews: Research testimonials and case studies from previous clients to gauge the quality of service.
Conclusion: Prioritizing Safety with Regular Fume Cupboard Testing
In conclusion, regular fume cupboard testing is a non-negotiable aspect of laboratory safety in Newport. By prioritizing this service, businesses not only protect their employees but also enhance operational efficiency and ensure adherence to regulatory standards. With the assistance of experts like Safe Plant UK, organizations can achieve a safer working environment that promotes innovation and research without compromising safety.
For comprehensive fume cupboard testing services in Newport, consider reaching out to Safe Plant UK today. Ensure the safety of your laboratory and contribute to a safer working world.
fume cupboard testing newport