MIG Power: Revolutionizing Cutting and Welding Equipment
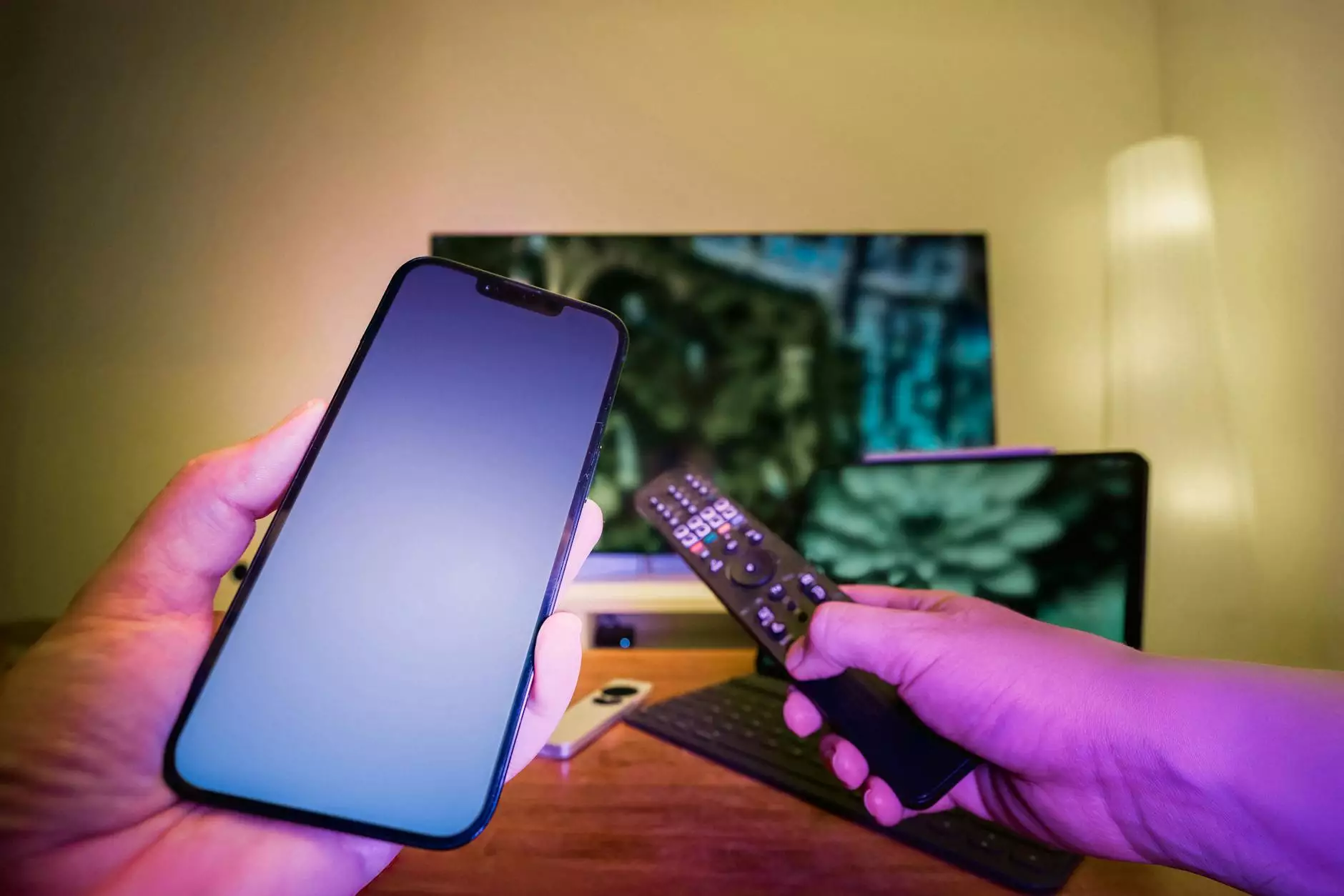
In today's rapidly evolving industrial landscape, MIG power is becoming increasingly crucial for manufacturers, fabricators, and DIY enthusiasts alike. It revolutionizes the way we approach cutting and welding, offering unmatched precision, efficiency, and ease of use. Understanding the intricacies of MIG welding and its equipment can unlock significant advantages for businesses that operate in demanding sectors. This article will delve deep into MIG power, examining what it entails, its benefits, its applications, and how it can elevate your operations by improving quality and reducing costs.
What is MIG Power?
MIG stands for Metal Inert Gas, a welding process characterized by its use of a continuous wire feed as an electrode and an inert gas to shield the weld area from atmospheric contamination. This versatile welding method is highly favored in the manufacturing of various products, particularly in the cutting and welding equipment industry. The combination of speed and ease makes MIG welding a go-to choice for both beginner and expert welders.
The Advantages of MIG Welding
1. Speed and Efficiency
One of the most notable advantages of MIG power is the speed with which it allows for welding operations. Unlike other welding methods that require multiple passes, MIG welding can often handle thicker materials in a single pass. This means:
- Reduced production time.
- Lower operational costs due to less workforce needed per project.
- Increased throughput, allowing businesses to take on more projects simultaneously.
2. Versatility
MIG power is not limited to a specific type of material. It can effectively weld a variety of metals, including:
- Aluminum
- Stainless Steel
- Mild Steel
- Bronze
This versatility is crucial for businesses that work with diverse materials, enabling them to utilize a single welding method for various applications.
3. Ease of Use
One of the significant advantages of MIG power is its intuitive operational process. The ease of setup and the relatively straightforward technique, which involves adjusting the voltage and wire feed speed, makes it accessible for welders at all skill levels. Moreover, with the proper training and practice, new operators can become proficient in a short amount of time.
4. Reduced Scrap Rates
With its precision and control, MIG welding significantly minimizes the amount of scrap material generated during the welding process. Accurate welding means better joints and fewer defects, leading to a more economical use of raw materials and improved profit margins.
Applications of MIG Power in Various Industries
The versatility of MIG power allows it to be widely used across various sectors. Below are some notable applications:
1. Automotive Industry
In automotive manufacturing, MIG welding is used for assembling vehicle frames and components. Its speed and strength can handle the rigorous demands of automotive production lines, ensuring that vehicles are constructed safely and efficiently.
2. Construction
The construction sector leverages MIG power for structural welding, where strong and durable joints are essential for safety. It is commonly used in erecting steel buildings, bridges, and other infrastructures.
3. Heavy Machinery
The heavy machinery sector utilizes MIG welding for fabricating equipment that can withstand harsh conditions. This includes everything from agricultural implements to mining machines, where reliability and strength are paramount.
4. Fabrication and Metalworking Shops
Many small to medium-sized fabrication shops utilize MIG power for custom fabrications. Its adaptability allows these businesses to take on diverse projects, whether creating unique metal pieces or repairing existing items.
Choosing the Right MIG Welding Equipment
Selecting the appropriate MIG welding equipment is vital for achieving optimal results. Here are some key considerations:
1. Power Source
MIG welders come in various power levels, suitable for different tasks. For industrial applications, consider a multi-process welder capable of handling diverse materials and thicknesses.
2. Type of Feed Mechanism
There are typically two types of wire feed mechanisms:
- Pull-feed systems: More common and efficient for most applications.
- Push-pull systems: Ideal for welding aluminum or softer metals where wire feed issues may arise.
3. Torch Quality
A good quality MIG torch will facilitate smooth operation and comfort for the welder. Look for ergonomic designs and reliable connections to enhance performance.
4. Additional Features
Features such as adjustable voltage, spool gun compatibility, and digital displays can greatly enhance the user experience and improve the outcomes of your welding tasks.
Conclusion: Embracing MIG Power for Future Success
As the demand for high-quality, efficient, and versatile welding solutions increases, embracing MIG power has become essential for businesses within the cutting and welding equipment sector. The unparalleled advantages it offers—speed, ease of use, and versatility—make it an invaluable tool for improving productivity and quality. By understanding MIG welding's capabilities and investing in the right equipment, businesses can efficiently prepare for a future where excellence and innovation are keys to success.